 |
|
01 |
30-11--0001
azaz????l????l ... |
.............................................................................................................. |
02 |
01-01-1970
No News Updates |
|
|
|
|
|
 |
|
|
|
|
|
In process Quality checks |
In process Formats include multiple criteria for compliance to Quality Parameters
The formats flow through out the manufacturing process to monitor defects in the product throughout process cycle
Check list prepared specific to
- inward inspection : of bare PCBs, Components, RM & consumables
- Process parameters : Dispensing, Stencil printing, Assembly, Temp. profiling of Reflow & wave soldering
- Final inspection : Criteria include specific customer inputs
- Testing : 100 % Test parameters tabulated as per Customer test procedures
|
In process Testing set up |
Component solderability tests
Component reliability tests on functional test
circuits
Tailor made pallets to identify missing components
Validation of Critical Processes viz. Component Placement And Soldering
In House Test jig fabrication set up for ICT & FCT specific to product test requirements
Mechanical tooling ,fixtures devised to get consistent result during cutting, bending ,forming operations
|
In house Test Jigs fabrication capability |
|
CAD net list ,Test Points generation.
Floor planning of physical layout of Test Set Up.
Matching test points & steps as per Test Procedures or sequence.
Placement of Test Pins for bed of nails ,fixture fabrication.
CNC data for mechanical fixing of test pins , bed of nails, receptacles ,support pins, guides.
Mechanical Assembly of test bench , wire wrapping , harnessing & soldering .
FCT –Instrument Panel , Electrical Measurements & Display.
ICT -Test programming as per BOM list , measuring parameters.
Forms or Formats to certify acquired data.
Pass & Fail report , Register, Log book. |
Test Methods : combination of MDA, ICT & FCT |
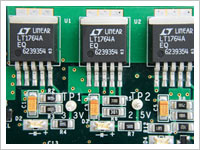 |
|
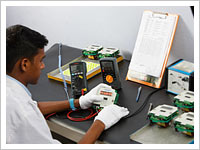 |
Manufacturing Defect Analysis |
|
Check list for Functional test procedure |
|
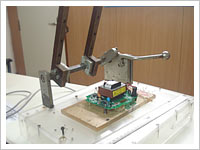 |
|
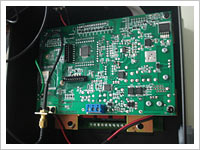 |
Customized Test Jigs |
|
System Ready for Final Functional Test |
|
Final Quality checking |
Product specific checklist prepared to ensure
Component orientation, height, mechanical dimensions and tolerances
Adhesion of bulky components to prevent damage due to vibration and transport
Re inspection of rework
Final inspection for Solder quality and manufacturing defects
Verification and approval of Functional Test reports
Traceability : Unique board identification number created
|
|
|
|
|